Clear thinking is far more important than hard work! For designers, it is essential to follow the design process. A standardized design process can avoid errors in the early stages that lead to major changes in the later design when dealing with complex circuits. Therefore, procedural design is necessary.
The following is a standardized PCB design flowchart. If you want to discuss more knowledge about PCB design
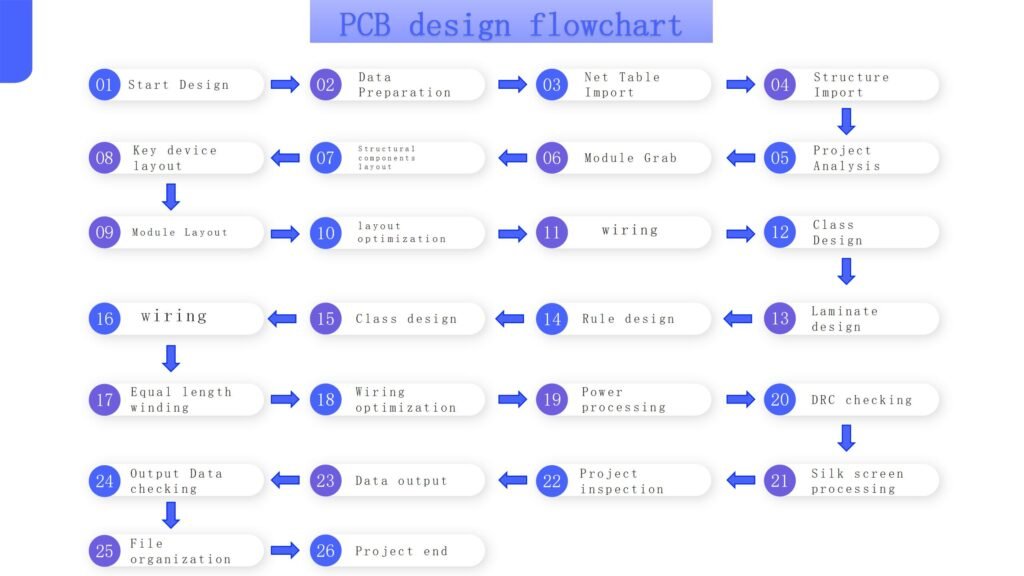
- Preparation content of materials
Before design, ensure that the following materials are prepared, and sufficient preparation of the materials can ensure the accuracy of subsequent PCB design and avoid the extension of the design cycle caused by repeated design.
1) Schematic diagram: The final version of the project design schematic diagram, please note that the pagination schematic diagram should be included in the project engineering;
2) Packaging library: PCB packaging library or component Datasheet file used to create a new packaging library;
3) Structure diagram: DXF structure file containing the main connector placement and height limit content;
4) Design Description: including key signal processing, special design requirements for chips, and board manufacturing process instructions;
5) Important device data manual: recommended layout and wiring for design reference.
- Import of Netlist
Import the schematic network connection and device packaging into the PCB to ensure there are no deviations in the import. If the schematic design is updated, be sure to import the latest schematic back into the PCB - Import of structure
Import the board frame, device positioning information, and other content into the PCB. If the structure is updated, be sure to re-import the latest structure diagram DXF into the PCB for verification. - Project Analysis
1) Principle block diagram: Analyze the main functions, modules used, and interface information of the entire project design, search for such module information, and understand its corresponding design requirements;
2) Interpretation of design instructions: including the processing of key signals, special design requirements for chips, and board manufacturing process instructions for easy integration into the corresponding PCB design;
3) Power Tree: Analyze the power supply situation of the entire project, and clarify the power flow direction, current size, and other situations, which are generally included in the schematic design, as shown in Figure 2. - Function module grabbing
Due to the increasing integration of products and the clear separation of most product functions, PCB design can capture the devices on the corresponding modules according to the schematic functional module page, facilitating designers to clarify the signal flow between functional modules in the later stage. Module auxiliary lines can be drawn inside the PCB board to evaluate the approximate position and occupancy range of the modules in the PCB, as shown in Figure 3. - Layout of structural components
According to the DXF structure file, import the board and frame, and place the devices with position requirements in the correct position. If there are structural updates, remember to update the structure as soon as possible to avoid duplication of subsequent work. - Key device layout
Placing the main IC in the appropriate position on the PCB according to the signal flow direction is actually a pre-layout of the PCB. Pre-layout can effectively plan the signal flow direction and PCB layout density balance of the overall PCB, improving the rationality of the layout. - Modular layout
Lay out the captured modules separately and place them in appropriate positions on the PCB. This section is a detailed PCB layout. Based on the pre-layout section, the layout is according to the layout requirements. Please refer to the module specifications in the following text for layout specifications, and pay attention to the location of punching and wiring. - Layout optimization
Fine-tune the already laid out components to make the entire PCB layout more reasonable and aesthetically pleasing - Cascade Settings
Based on the flying wires after PCB layout, it is necessary to estimate the number of PCB layers required for the design. Based on the number of layers and board thickness, use stacking software (or based on existing stacking templates) to calculate the line width and line spacing. - Rule Settings
Set up line width and line spacing rules on the PCB for easy wiring. The rule settings need to be checked against the design requirements and the process requirements of the board factory, otherwise, it may result in the entire rewiring. - Class Settings
According to the IC signal requirements, group the signals with design requirements, set them into different classes, and set corresponding class rules. - Wiring
Connect the signals of the same network, and after the wiring is completed, it is necessary to verify the entire PCB wiring requirements, check the power supply wiring, and confirm whether it meets the current carrying requirements and various certification requirements. - Equal length winding
Perform equal-length processing on the signal lines required by the time sequence, and pay attention to the error requirements of the signal during equal-length processing. - Wiring optimization
Optimize the connected wiring to make it more beautiful and reasonable. Check the key signals and follow the optimal processing. - Power processing
This step is mainly to optimize the power signal in the single board and divide the power plane to confirm that the current carrying requirements are met. When dividing the plane, pay attention not to cross the important signal lines, as shown in Figure 4. - DRC inspection
1) Connectivity check: Check if all signals in the project are connected and there are no open circuits;
2) Other inspections: Check whether there are short circuits in the signals in the project, whether there are contents to avoid prohibited areas, and to avoid device restrictions. - Silkscreen processing
Reasonably arrange the device tag number screen on the PCB, add corresponding version numbers, production identification (anti-static, SN number, enterprise logo, etc.), and pay attention to the convenience of production and readability when placing the screen. - Project inspection
Finally, verify all the design requirements of the customer and check the production process. - Photo output
Set up and output Gerber photo files in EDA software. If it is a product of the same type, you can set templates for Gerber output to facilitate one-click output during the next update. - Photo inspection
Although EDA tools have conducted effective DRC checks on the designed PCB, the output Gerber should also be checked for manufacturability issues on production tools in some industries, which can help solve production problems during the design phase. It is recommended that tools such as Huaqiu DFM check the output photo files. - File archiving
A good design file archiving can help us effectively improve communication and data transmission between departments and departments. Based on experience, it is recommended that designers archive files as follows
1) ASM folder: contains assembly files, top and bottom assembly drawings, for customers to assemble components → send to the SMT factory
2) CAM folder: Contains photo files, IPC netlist, PCB production instructions → Send to PCB manufacturing or SMT factory
3) DXF folder: Contains the structural diagram files used in the project → Send to the structural engineer
4) PCB folder: Contains the final PCB files of the project → Engineering designer revisions and designs
5) SCH folder: Contains the final schematic files of the project → Engineering designer revisions and designs
6) SMT folder: Contains patch coordinate files and steel mesh files → Send to patch factory